Updating your Standard Operating Procedures
The PI, delegate, or lab member determines if your SOP needs to be reviewed.
An SOP needs to be reviewed if any of the following events have happened:
- The nature of the hazard changes. For example, a previously unknown hazard is identified, use of vacuum or pressure has changed, there is an increase/decrease in temperature, etc.
- Any chemical-related changes. For example, new chemicals are added to the inventory, a quantity increase or scale-up, an increase in concentration, new chemical supplier, etc.
- The equipment changes.
- An unexpected outcome occurs, like an unanticipated rise or fall in temperature, increased gas production, unexpected color change or phase separation, etc.
- At a minimum, every three years.
If one of the above triggers has necessitated the reviewing of your SOP, review it for content and chemical listings. Make any necessary changes. If a specific chemical on your SOP is no longer relevant, you have the choice to keep in on the SOP or remove it. If you may get it back in the lab consider keeping it (to minimize the need for updating and retraining later). If you are certain you will never use or order the chemical again, consider removing it.
During the review process consider whether the SOP still needed: if an SOP is no longer relevant, please remove it from your safety binder and store it where you can find it if Cal/OSHA asks for it.
Once the SOP has been updated, update the version history in the “Lab-Specific Revision History” section. It should look similar to this:
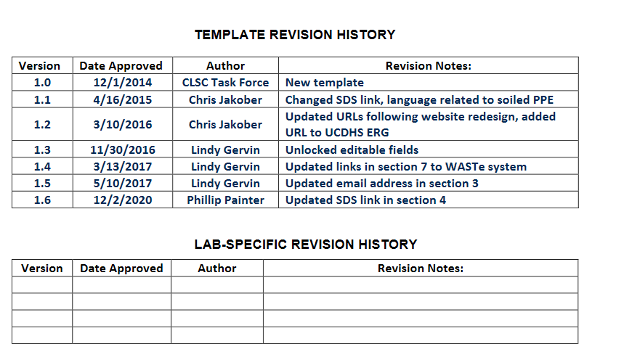
If you made changes update the version number, the date, and your name. Type in any revisions: include any major changes including but not limited to what was updated in the chemical list and/or the exact update that you did.
Also include in the revision history if the SOP was reviewed but no updates were required.
Retrain on the new SOP. If significant changes are made beyond grammar and spelling errors, everyone will need to be retrained. Note: researchers need to be retrained on the SOP every three years even if there were no changes to the SOP.
Finally, place the new version of your SOP in your safety binder with the new training. The retired version of the SOP should be removed from your safety binder and stored somewhere where you can find it if Cal/OSHA asks for it.
Additional notes
- For more information about SOPs, see the Laboratory Safety Manual (LSM), Chapter IV. C. 2 b Standard Operating Procedures (Page 40-42 of version 1.6 of the LSM)
- SOP templates can be found here: safetyservices.ucdavis.edu/units/ehs/research/chemical/sop-templates
- Please note the addition of chemicals to an SOP is considered a major change and requires re-training.